Quality management
Consulting QM System
QM stands for “quality management” (QM) and refers to the practices, processes and systems implemented with a management system to ensure and continuously improve the quality of services, products and operating procedures. The aim of quality management is to achieve and maintain the highest standards in terms of quality, efficiency and customer satisfaction.
We support you in complying with QM requirements in your company
We at ferrolog are your partner when it comes to the quality management system in your company! Do you need a partner who can support and advise you in the creation and maintenance of your QM system?
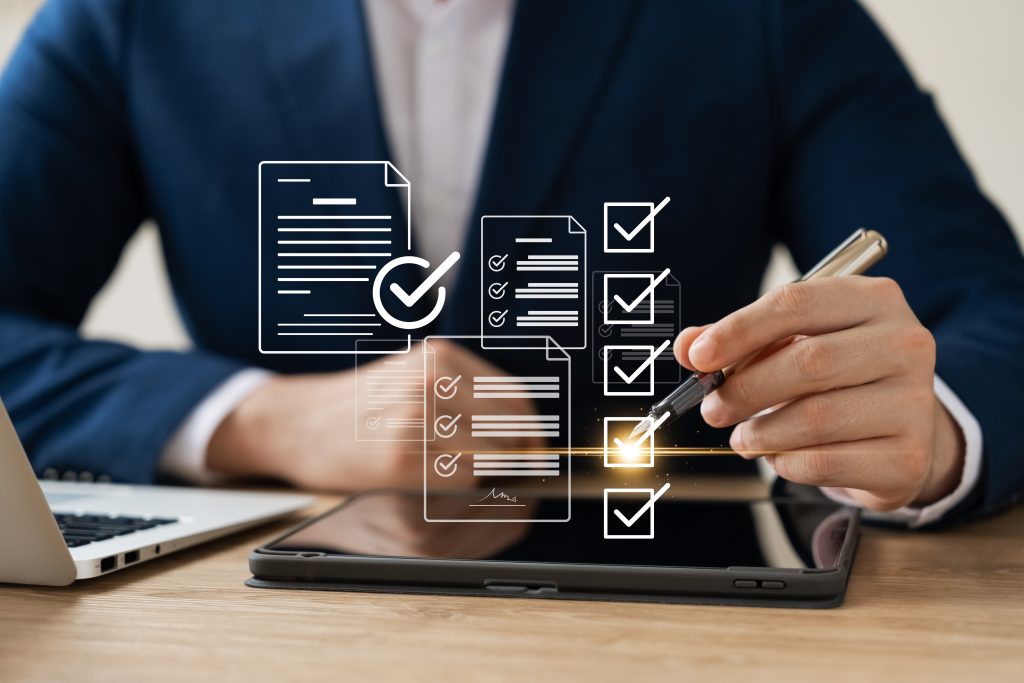
How can we support you in quality management?
- Assumption of the function of the responsible (external) project manager and contact person for the company vis-à-vis the responsible accredited body for all matters relating to the project to obtain certification
- Development of a quality management system in line with requirements on the basis of standard-compliant samples and templates
- Editing and creation of QM procedures and proposals for associated documents such as QM manual, forms, process descriptions, procedural instructions, work instructions, checklists, questionnaires, training plans, competence matrix, CIP list, legal register and the like to the extent required
- Preparation of application documents and support with the submission of applications to the accredited body
- Participation in a preliminary meeting with the accredited body on the basis of the documents approved by the client (= so-called stage 1 audit) and in the certification audit (stage 2 audit)
- Examination of all correspondence and documents of the accredited body and, if necessary, preparation of lists of measures to be processed and processing of any letters of improvement
- Preparation and implementation of an internal audit in the area of ISO 9001 incl. Preparation of an audit report
Quality management system - what is it anyway?
A quality management system (QMS) is a comprehensive and structured system of processes, guidelines, procedures and resources implemented in an organization to plan, control, monitor and continuously improve the quality of products or services. The main objective of a QMS is to ensure that an organization’s products or services meet the defined quality standards and meet or exceed customer expectations.
Here are some important features and aspects of a quality management system:
- 1. quality policy and objectives: The organization develops a quality policy that reflects its commitment to quality and customer satisfaction. Targets are set in order to implement this policy and achieve the quality standards.
- 2. process management: A QMS comprises the planning, implementation and control of processes that are used in the organization to produce or provide quality products or services.
- 3. risk management: risk assessment and management procedures can be integrated to identify and minimize potential quality problems.
- 4. quality control and testing: The QMS contains procedures for monitoring and testing products to ensure that they meet quality standards. This can include inspections, tests and audits.
- 5. documentation and records: All processes and procedures within the QMS are documented and recorded to ensure transparency and traceability.
- 6. continuous improvement: A central principle of a QMS is continuous improvement. The organization regularly analyses its processes and results in order to identify and implement opportunities for improvement.
- 7. customer satisfaction: meeting customer requirements and ensuring customer satisfaction are at the heart of a QMS. Feedback from customers is recorded and used for improvement.
- 8. training and qualification: Employees are trained and qualified to understand the quality standards and implement them in their work.
- 9 Compliance: A QMS can ensure that the organization meets legal and regulatory requirements.
Quality management systems are used in a variety of industries and organizations. They are a key tool for ensuring the quality of products and services, reducing risks and continuously improving the organization as a whole. A well-known standard for quality management systems is EN ISO 9001.
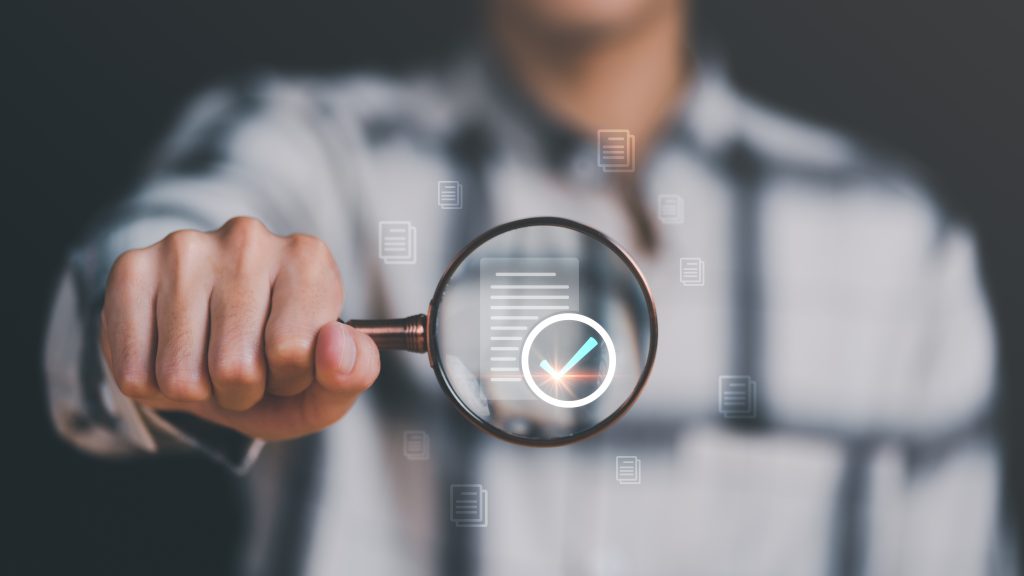
Quality standard: ISO 9001
ISO 9001 is an internationally recognized standard for quality management systems (QMS). It was developed by the International Organization for Standardization (ISO) and defines the requirements for the implementation and certification of an effective quality management system. ISO 9001 is the most widely used quality management standard in the world and is used by organizations in various industries and sectors around the world.
ISO 9001 is based on a Plan-Do-Check-Act (PDCA) cycle that promotes continuous improvement. It is divided into several sections, including:
- Context of the organization: This is where the organizational goals and the relevant internal and external factors are defined.
- Leadership: This is about the commitment of top management to quality management and the definition of quality guidelines and objectives.
- Planning: This section deals with the identification of risks and opportunities, the definition of quality objectives and the development of quality plans.
- Support: Resources, training and communication in quality management are dealt with here.
- Operations: This section deals with the implementation of processes and procedures to fulfill the quality objectives.
- Performance evaluation: This is where the performance of the QMS is monitored and measured.
- Improvement: This section defines how organizations take measures for continuous improvement.
What are the advantages of ISO 9001?
Implementing ISO 9001 can offer numerous benefits, including increased customer satisfaction, increased efficiency, better process control, risk management and the ability to access global markets.
Quality assurance systems for the satisfaction of all stakeholders!
A quality management system (QMS) that meets the standards of the series of standards offers a way to lead a company safely into the future, even in times of change and changing circumstances. It enables the control and assurance of quality in a company, even if the conditions and requirements change.
ISO 9001 certificates symbolize a high standard for customers, suppliers and employees alike and help you to comply with important systems and regulations.
We are your partner for environmental management in your railroad company!
What else can we support you with?
Support with an integrated management system, incl. the following standards:
SMS
Safety management in railroad operations
ECM
Entity in Charge of Maintenance
SGA
Health & safety at work
Railway Operations
Personnel placement
e.g. train driver, wagon master, etc.
Maintenance of rail vehicles
Maintenance Management
ferrolog is your partner for quality management!
No matter which standards you have to comply with – we do our part to ensure that you can successfully comply with the relevant regulations! Get in touch with us!